Record demand for its innovative Claydon Opti-Till® agricultural crop establishment machinery has led progressive family-owned UK manufacturer Claydon Yield-o-Meter Ltd to further expand its factory in West Suffolk. And demand is still rapidly increasing. The completion of a new purpose-built building at the site in Wickhambrook will more than double production capacity and create additional jobs.
Supported by a £267,400 Growing Business Fund Grant from the New Anglia Local Enterprise Partnership (NALEP), the project will help the 40-year-old company to meet an exponential increase in orders. These are expected to grow further in 2023 as the business works with its dealer and distributor partners in existing and new markets to develop sales of its Evolution and Hybrid drills, Straw Harrows, TerraStar® light cultivators and TerraBlade inter-row hoes.
“Unlike many other companies in the UK farm machinery sector which import machinery made overseas we design, test and manufacture all our products from scratch, employ local staff and benefit the UK businesses which supply us,” explains Chief Executive Officer Jeff Claydon.
An arable farmer, Mr Claydon founded the company in 1981 to manufacture the Claydon Yield-o-Meter, the first device to provide an accurate ‘real-time’ reading of crop yields on a display in the cab of a combine harvester. In 2001, when grain prices fell to levels which made combinable crop production uneconomic using traditional establishment methods, Jeff developed the Opti-Till® Direct Strip Seeding System to reduce costs without adversely impacting output, thereby securing the future of his family’s farm.
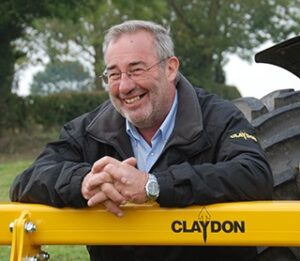
Jeff Claydon, CEO, Claydon Yield-o-Meter Limited
Today, farmers all over the world are saving the equivalent of up to £250 per hectare on the cost of establishing combinable crops across the widest range of soil types and conditions using Opti-Till®, which combines stubble management and strip seeding techniques that have been proven over 20 years. Compared with traditional methods, they enable farming businesses to operate much more efficiently, profitably, and sustainably, using just 10 per cent of the fuel required for a traditional plough-based system, with significant yield, soil fertility and environment benefits.
Claydon has seen demand for its products grow ten-fold since 2010. With many markets still at an embryonic stage and its distribution network growing rapidly the company expects sales to grow exponentially during 2023, despite the undoubted challenges. Like many other UK companies, Claydon is having to deal with the ongoing adverse effects of Brexit, which has made transporting its products to Europe considerably more difficult, time consuming and expensive.
Expanding to meet demand
In 2015, Claydon was awarded the New Anglia Local Enterprise Partnership grant to help the business develop in three stages. The first of these was the construction of new offices adjoining the company’s existing production facility to house additional staff to support customers in the UK and overseas markets. Planning permission was awarded in March 2016 and work started in July the following year, with Claydon employees completing the ground works, construction and fitting out of the building involving suppliers and contractors from across the Anglia region.
Blending in with the existing workshop building and surrounding countryside to minimise their visual impact, the two-storey offices provide 365m2 of accommodation for up to 27 full and part-time staff on the top level. The ground floor is dedicated to visitors, with two meeting rooms, a dealer training and presentation studio which can accommodate 50 people, together with commercial-grade catering facilities. A £100,000 investment in solar technologies provides 100kW/h of electrical energy, reducing the use of electricity from the National Grid at the site and minimising the company’s carbon footprint.
The second stage in the company’s development, which has just been completed, involved the construction of a new assembly building on the footprint of derelict former farm buildings and is much needed, Mr Claydon states.
“The company is growing rapidly and massively, a highly skilled team is in place, but additional production capacity is needed to manufacture Claydon Opti-Till® products to fulfil demand from markets all over the world, including the UK where sales have doubled. Momentum is building strongly, helped by our presence at overseas trade shows, together with the ongoing expansion of our global network of importers, agents, and dealers in 22 countries, whose local knowledge and support gives potential customers confidence to invest in UK-manufactured products.
“Despite huge uncertainties caused by Brexit and Covid-19, in July 2021 we decided to go ahead with the new building to mark the company’s 40th anniversary. Claydon staff completed the footings in the winter of 2021 and construction started in summer 2022. The project was managed in-house but, due to difficulties in obtaining contractors and materials, progress was slower than anticipated.”
“This significant investment we have made in these new production facilities will help us to take a quantum leap forward to meet demand for Claydon products and is a key part of our long-term plan to develop the potential which exists all over the world,” said Mr Claydon.